Maxcaster
Ultimate flexibility and accuracy for every application
We have continually improved the slipformer technology over the past decades. It is the perfect solution whenever many different concrete products are to be produced with just one machine: Prestressed hollow core slabs, solid slabs, T-beams, lintels, ram piles, vineyard posts, TT slabs, ribbed slabs and much more. After a conversion time of < 10 minutes, the machine insert module is exchanged and another product is manufactured. The modular machine concept allows the production of all commercially available prestressed concrete elements up to 240 cm wide and up to 50 cm high.
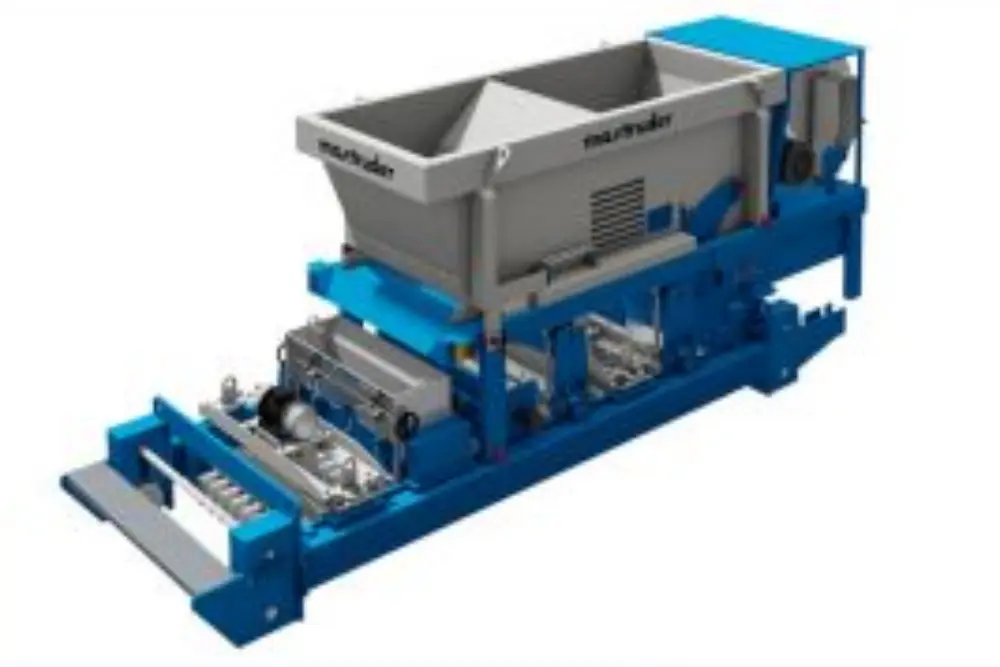
Compaction System
The maxcaster slipformer produces in a continuous casting process. Concrete is poured in and shaped into the desired form in up to three stages. For concrete compaction, we use a powerful combination of tamping, high and normal frequency vibrators. This allows the use of a very dry, earth-dry concrete with a low water/cement ratio. This results in a low cement requirement of about 320-400 kg/m³ of concrete. The end products achieve a compressive strength of up to 75 MPa and can usually be cut after less than 8 hours of curing time.
High-density concrete – Minimum cement consumption – Maximum productivity
10 min. conversion time
< 8h Short Curing Time
Modular design
The maxcaster consists of three main modules: the chassis module with travel drive unit, the feeder module with concrete silo and power unit, and the machine insert module with formwork. Each of the main modules is subdivided into different sub-modules. Result: lots of combination possibilities.
Highest variability – Shortest changeover times – Minimum space requirement
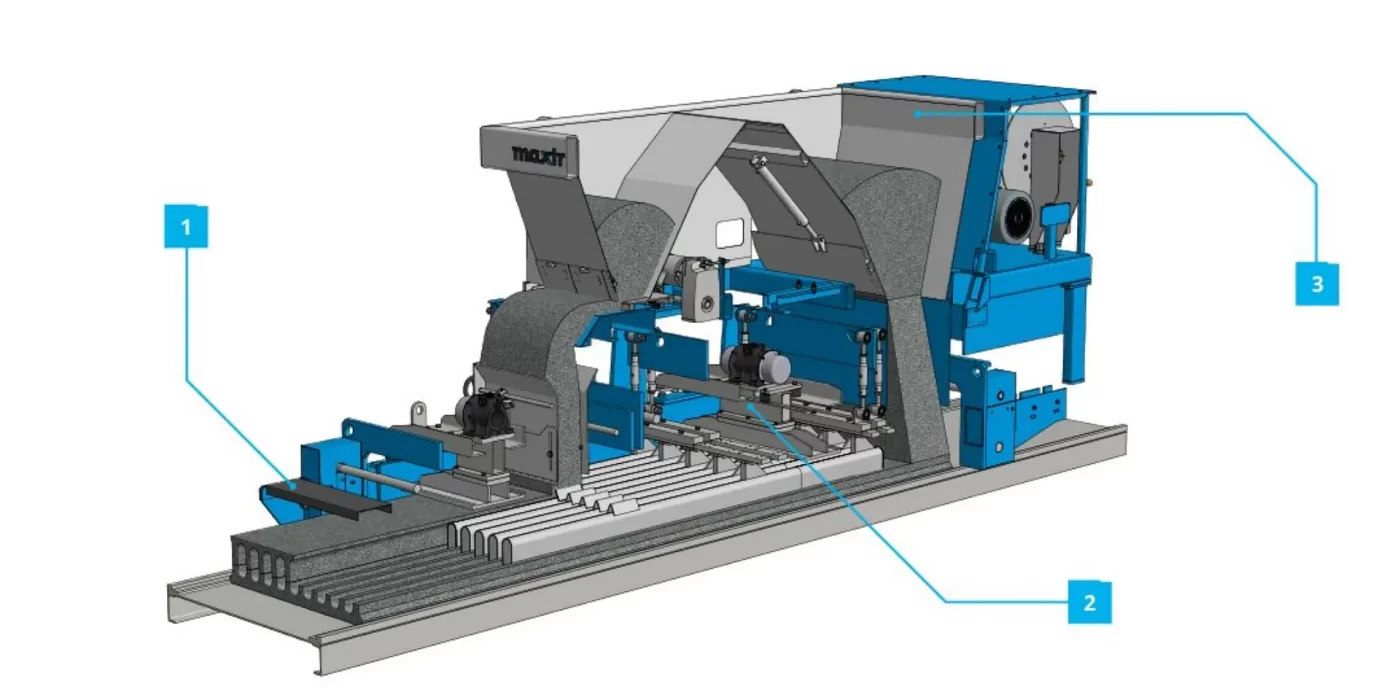
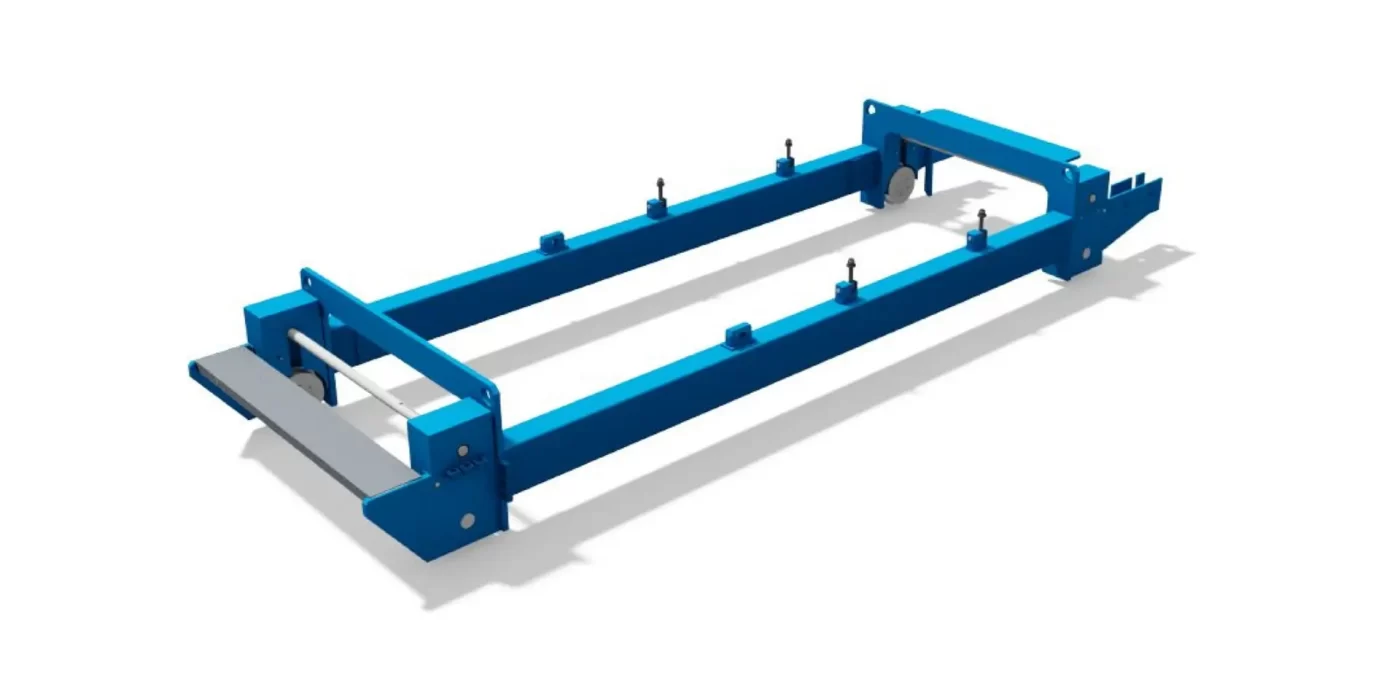
1. CHASSIS MODULE
Stiff chassis with powerful 4 wheel drive, tool-free installation of the universal feeder unit module
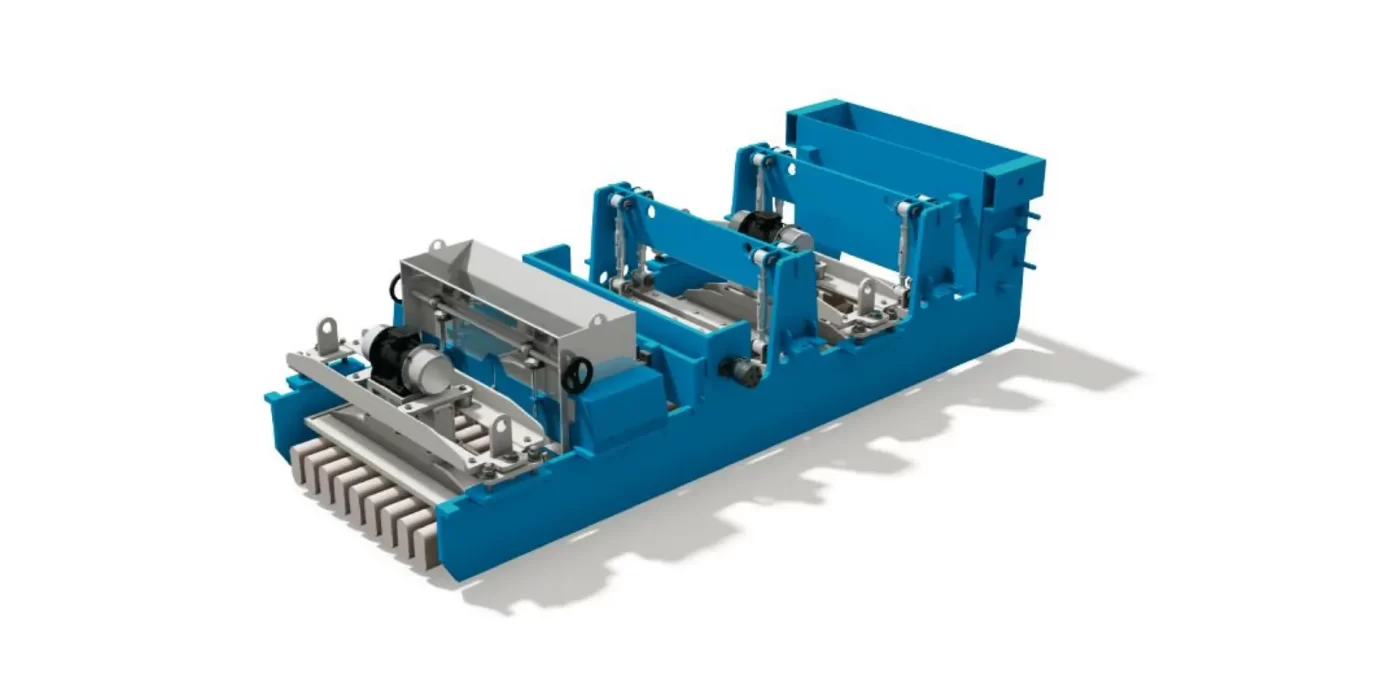
2. MACHINE INSERT MODUL
Quick exchange machine insert with formwork according to each product. Conversion time <10 min for minimum down times
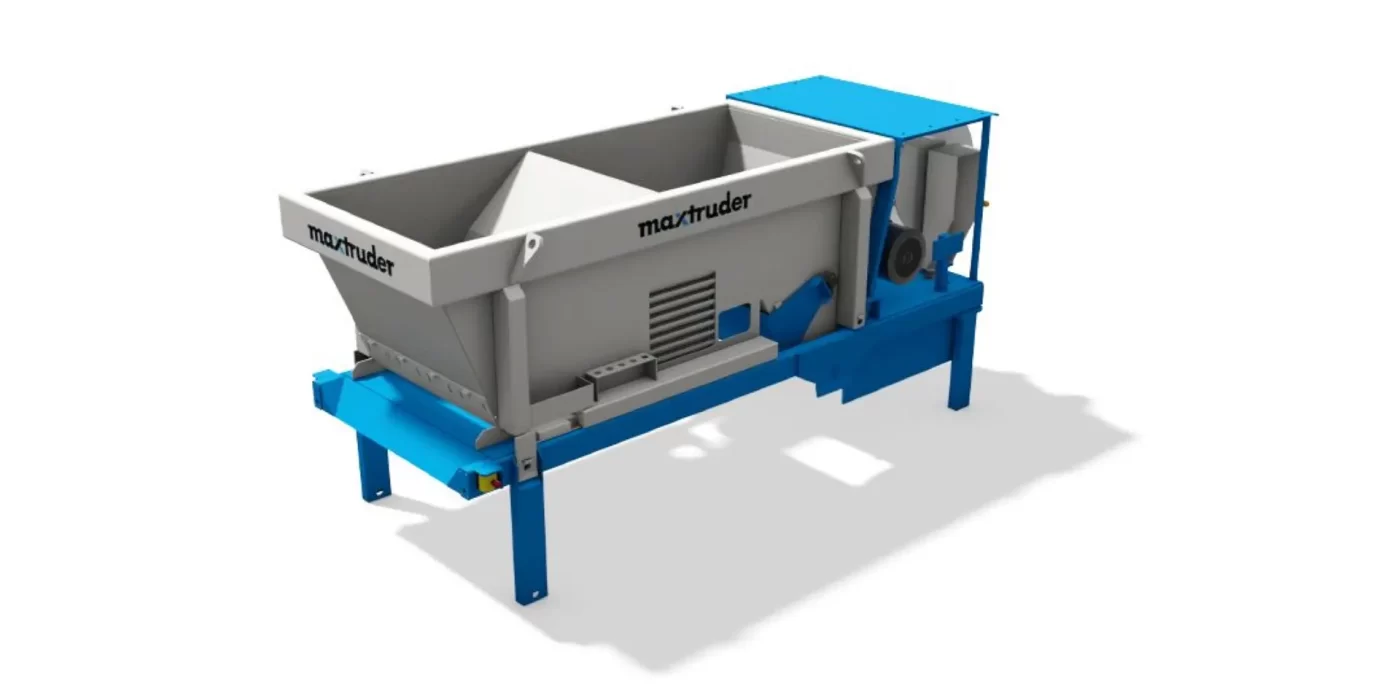
3. FEEDER MODULE
Feeder module with electric power supply, hydraulic aggregate, operator interface and 1, 2 or 3 stage concrete silo
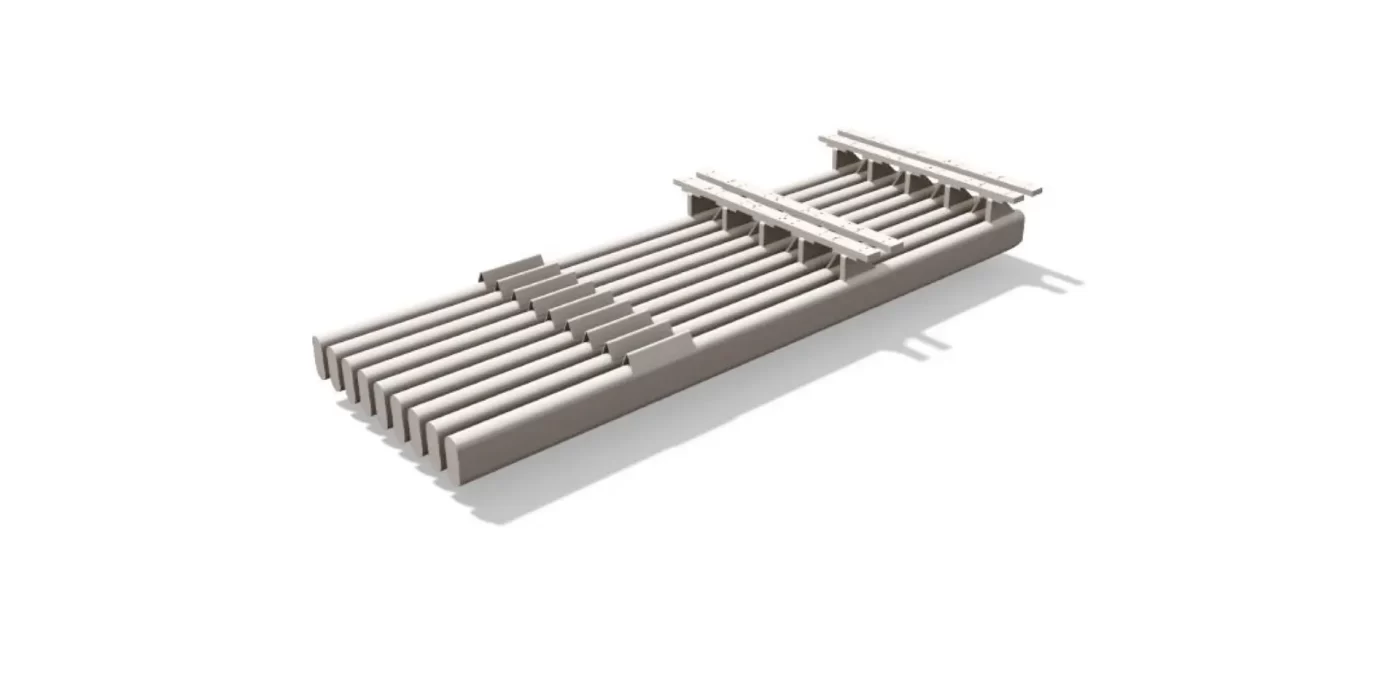
OPTIONAL
COREMOULD- AND FORMWORK CASSETTE MODULE
Complete module for quick exchange in the machine insert
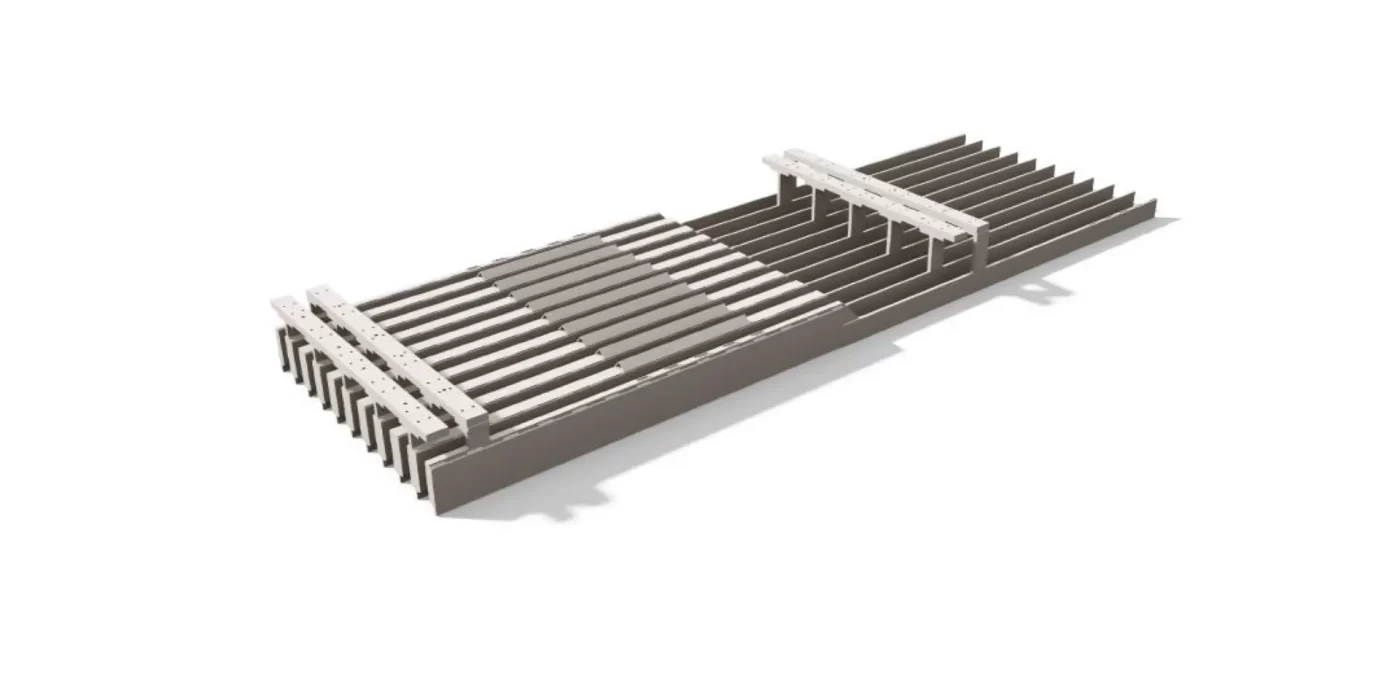
OPTIONAL
FORMWORK MODULE
Individual modules to combine in the formwork cassette
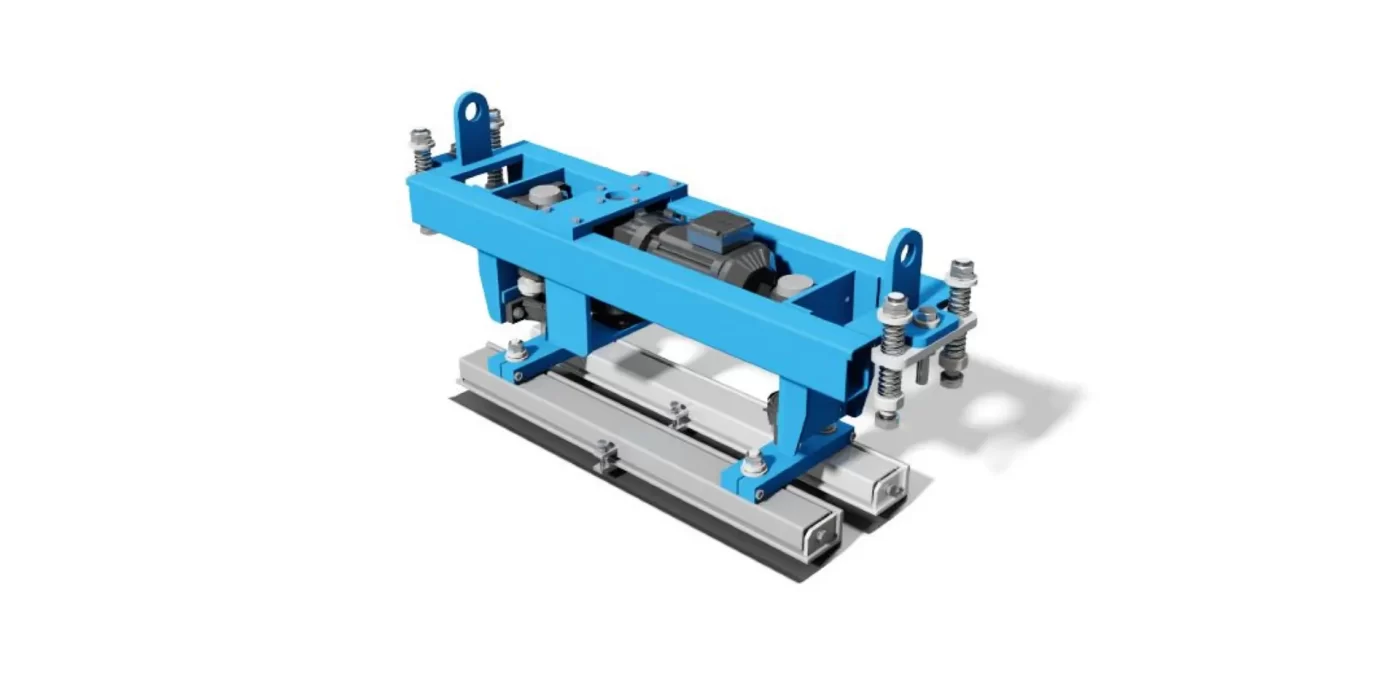
OPTIONAL
SMOOTHING MODULE
Electromechanical smoothing module, for automatic smoothing of hollow and solid slabs, wall panels
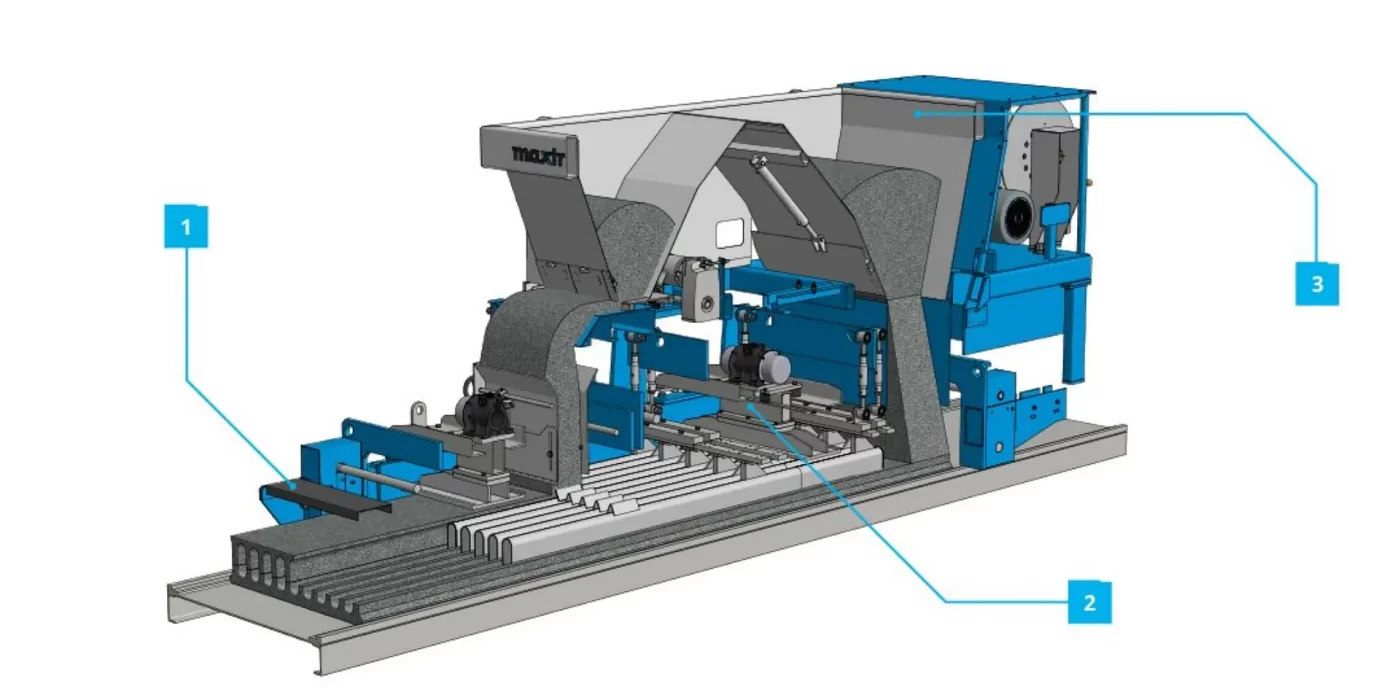
HIGHEST FLEXIBILITY
- Largest product variety of prestressed concrete elements
- Multi-level modular quick-change system
- Changeover < 10 minutes
USER-FRIENDLY
- Intuitive operation, easy understandable machine concept
- Quick and easy cleaning due to simple module separation
- Particularly robust and durable
HIGHEST PRODUCT QUALITY
- Oscillating formwork system for consistently superior concrete product quality
- Powerful compaction with concrete strength up to 75 MPa and perfect tension wire bond
- Perfectly accurate end products with ready-to-paint underneath
Large Product Variety
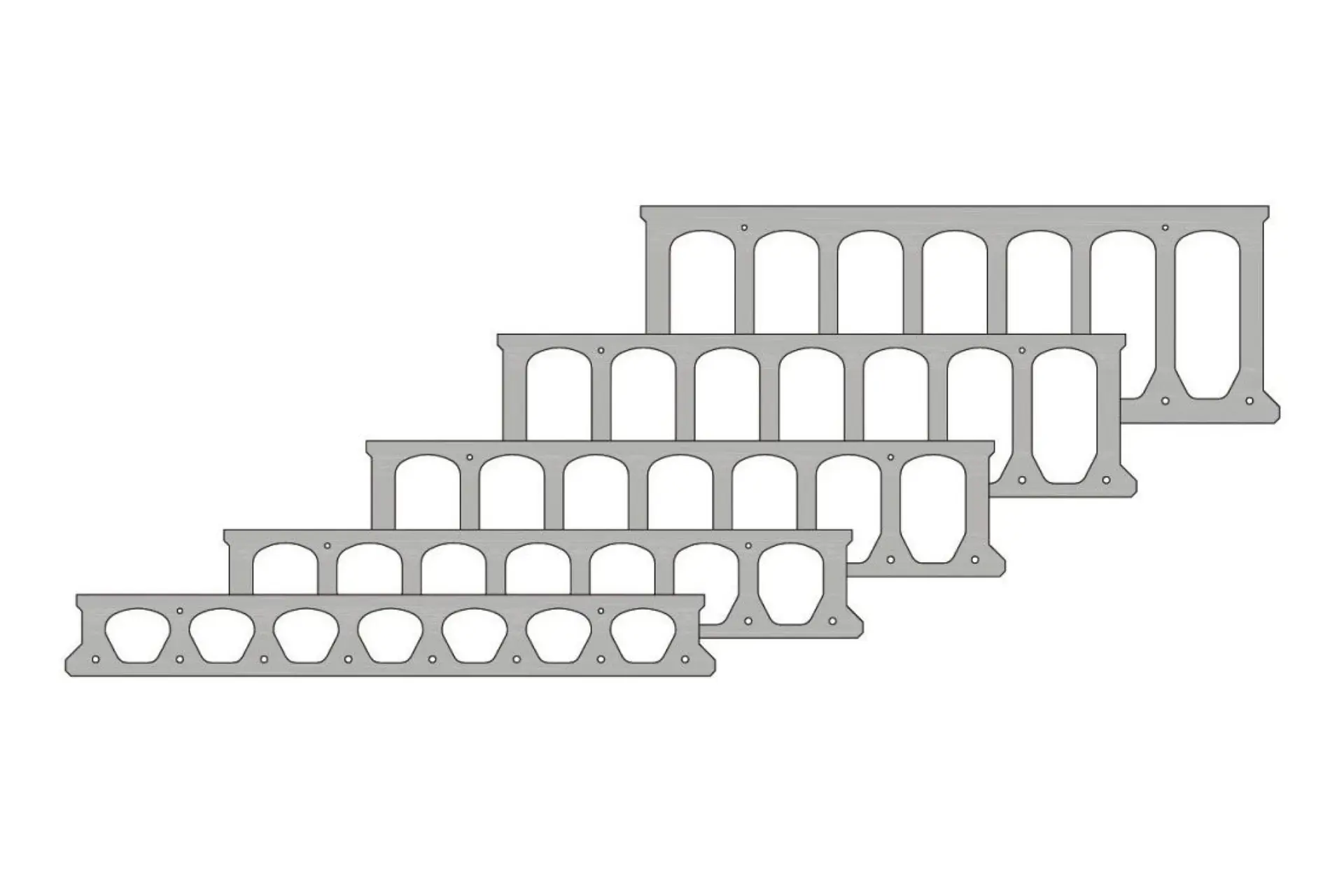
HOLLOW CORE SLABS
– Solid slabs, hollow core floor slabs and wall elements
– 7 to 50 cm thickness, 30 to 240 cm width
– Void ratio up to over 50%
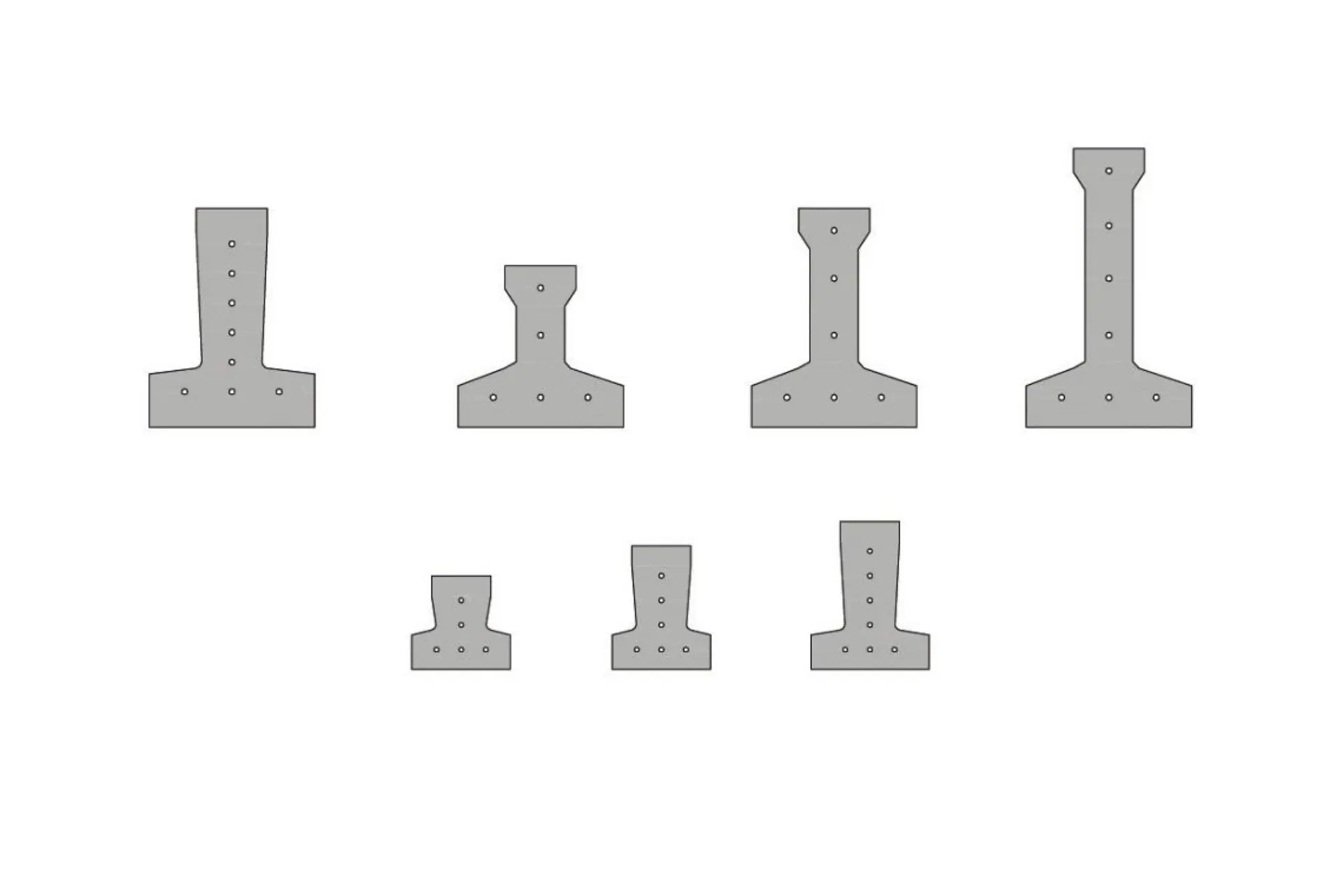
T-BEAMS AND I-BEAMS
– Invertied T-beams and I-beams
– Simultaneous production of up to 12 beams.
– Production speed up to 3,5 m/min
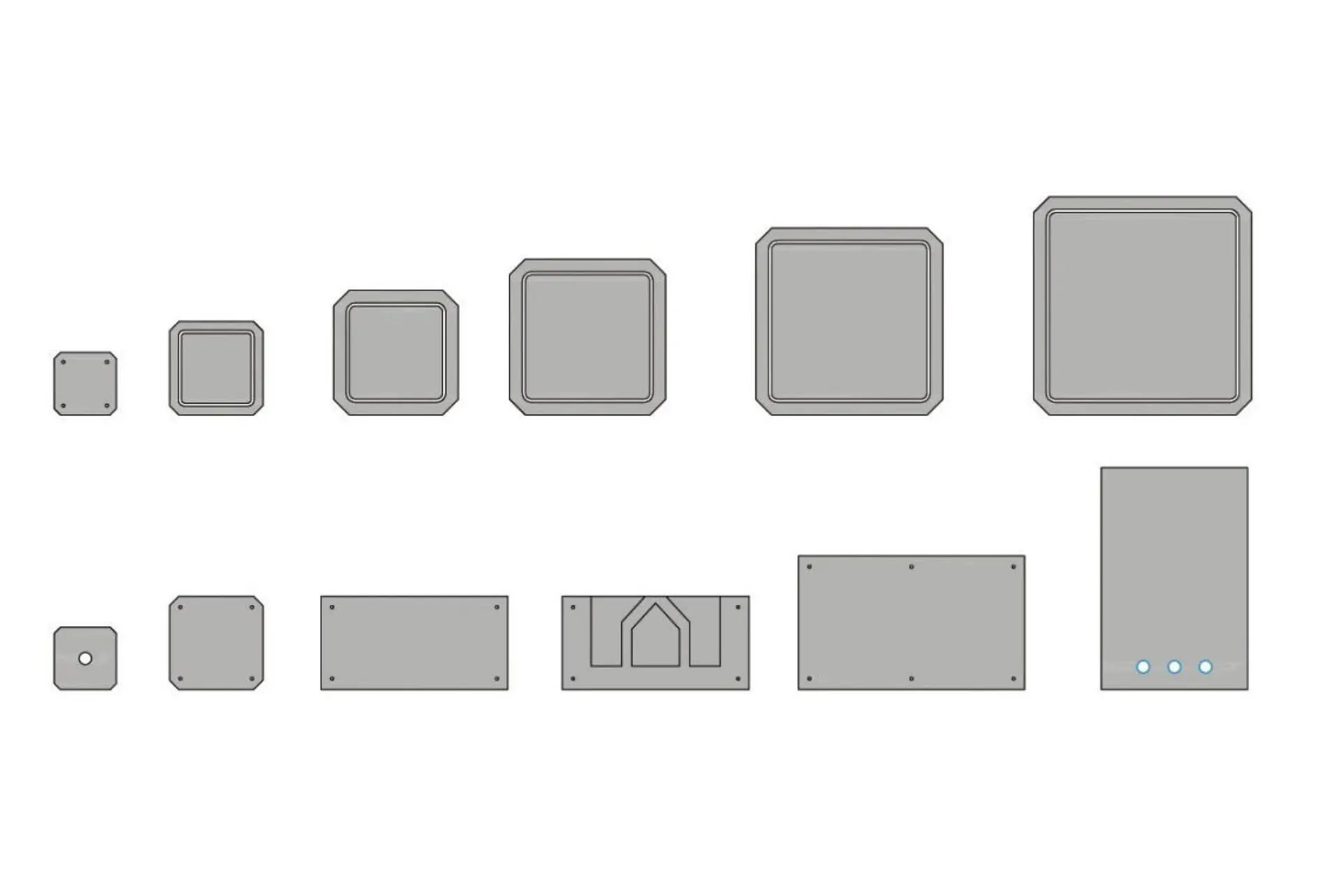
BEAMS, LINTELS, RAM PILES
– Fence posts 4.5 x 4.5 cm
– Ram piles up to 45 x 45 cm
– Lintels, vineyard posts…
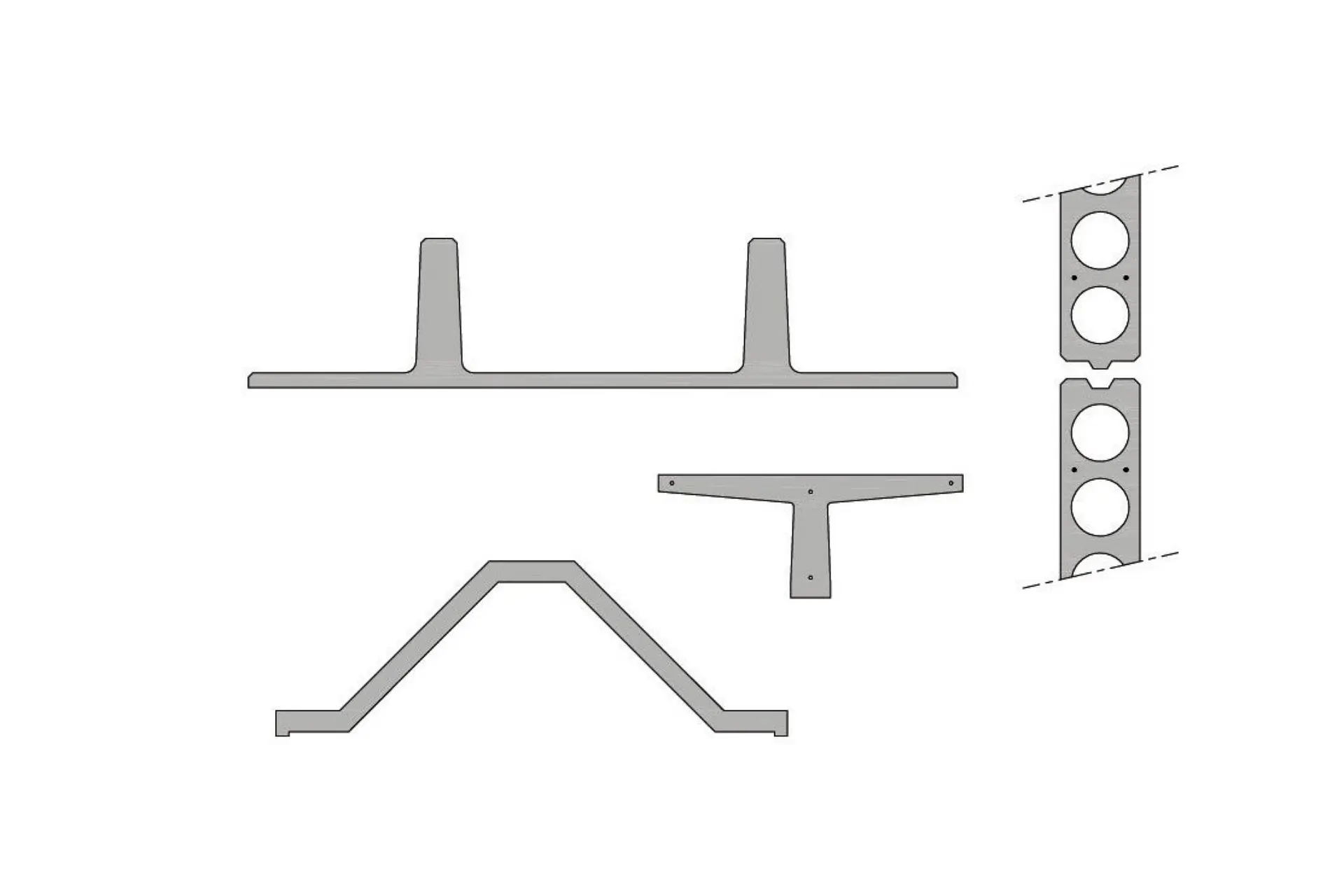
TT-SLABS AND RIBBED SLABS
– TT-slabs, solid or insulated U channels
– Ribbed slabs and V elements
– Noise absorbing wall elements